IKB®
the rupture disc with the patented manufacturing process.

Superior performance and minimal downtime with advanced CPL™ Technology.
Suitable for a wide range of process conditions, the IKB® is a cost-effective, reverse acting rupture disc that is suitable for a variety of applications. The IKB® is the only reverse acting rupture disc to be manufactured using REMBE®’s unique Contour Precision Lasering™ (CPL™) Technology ensuring high quality, accurate burst control even in the harshest of environments.
The IKB® rupture disc was developed to provide reliable protection against excessive overpressure and vacuum in equipment such as pressure vessels, pipe systems, gas cylinders and reactors. It is suitable for applications with gas, steam and liquids* as well as for isolating safety valves. IKB® permits a standard operating ratio of up to 95%**. The patented manufacturing process produces an instant, full and fragmentation-free opening across the full width of the vent. A high quality rupture disc produced without the need for mechanical scoring or knife constructions. This ensures exceptionally high resistance even under cyclic loads. The extremely simple installation of a suitable rupture disc holder is torqueindependent and requires no special tools.
* If there is a gas cushion upstream of the rupture disc.
** Depending on the specific application.
** Depending on the specific application.

signaling devices
Automated processes use intelligent signaling systems to keep you informed at all times about the status of your entire plant and any faults that may arise. You can even install signaling devices for rupture discs that have already been installed.
rupture disc holder
REMBE® guarantees you a perfect installation and optimal function of your bursting disc. Due to the special design of the various REMBE® rupture disc holders, incorrect installation of the associated rupture disc is impossible.
Fast, safe, installation for maximum process uptime.
The IKB® is a solid-metal, torque independent design**, enabling simpler installation and routine maintenance checks. REMBE®’s torque independent solutions minimise the risk of damage due to incorrect handling or during improper installation, ensuring reliable burst pressure relief and minimal downtime. CPL™ Technology ensures a smooth process face, reducing any concerns of corrosion or contamination, making the IKB® a versatile solution for a wide range of industries. The IKB® is fully compatible gas, steam or liquid***, including under full vacuum conditions.
** Low pressures may require a specific torque value. Please consult the REMBE® operating manual.
*** Gas cap must be present.
*** Gas cap must be present.
Reduce pressure relief expenditure.
The IKB® is perfect for new installations, combining superior performance with cost-effective pricing. The torque independent IKB® is ideal for commissioning where several rupture discs are installed in a short space of time, as no special tools or training is required. The IKB® can be installed quickly, safely and easily, ensuring no delays to start-up. Available in a wide range of materials and coating options the IKB® is an excellent choice for relief valve isolation. Selecting the IKB® at project specification stage, can provide significant cost benefits, not only in the product itself, but by enabling a pressure relief valve to be sourced in a standard material as the valve is not in contact with the process medium.Installed into the IG-KUB® holder, which is also compatible with REMBE®’s unique reverse-acting solution – KUB® allows the possibility to upgrade without further outlay in a new holder if process conditions were to change in the future. Used together with REMBE®’s NIMU detection system for a full rupture disc assembly, ensuring fail safe installation and notification of disc burst site wide.
Advantages
-
Maximum safety even at high pressures.
-
Use of safety valves made of less expensive materials is possible as they do not come into contact with the medium during normal operation.
-
In-situ tests reduce safety valve maintenance costs.
Technical data
Product parameters
Feature | Characteristics | Variations |
---|---|---|
Signalling available | ✓ | NIMU, SIGU, BT-S, FOS, SB(-S), SGK, SBK-S |
Safety valve isolation | ✓ | - |
Tolerance | % | ± 10 (±5, -0/+10, +0/-10 upon request) | - |
Manufacturing design range | % | 0 | - |
Operating ratio | % | 95 | - |
Non-fragmenting design | ✓ | - |
Temperature range | °C | -80 to 600 * | - |
Leakrate | mbar l s-1 | 10-4 to 10-6 | - |
* Depending on the specific application.
Applications
-
autoclaves
-
chemical industry
-
chemical reactors
-
condensers
-
cryogenic applications
-
cryostats + transport containers
-
desalination plants
-
distillation towers
-
flare stacks
-
food production
-
FPSO applications
-
gas compressor modules
-
gas turbines for power generation
-
gas-tight pressure vessels
-
geothermal energy
-
hazardous goods containers
-
heat exchangers
-
intermodal containers for corrosive / aggressive media
-
isolation of safety valves
-
LDPE (thermoplastic)
-
LNG
-
mixers
-
oil and gas separation and treatment
-
petrochemical plants
-
power plants
-
process vessels
-
reactors
-
refineries
-
reverse osmosis systems
-
separators
-
spray dryers
-
sterile tanks / aseptic tanks
Industries
-
aerospace
-
brewery
-
chemical- petrochemical
-
food
-
hydrogen
-
oil and gas industry
-
pharmaceutical industry
Process medium | Suitability |
---|---|
Gas | Steam | ✓✓ |
Liquid with gas cushion | ✓✓ |
Two phase flow | ✓ |
Hygienic applications | ✓✓ |
✓✓ recommended
✓ suitable
✓ suitable
Certifications

Works Certificate

DGRL

ASME

KOSHA (South Korea)

CML (China)

TR CU (EEU)
The IKB® is quick, safe and easy to install and enables your system to be commissioned quickly.



Click and drag image to view.
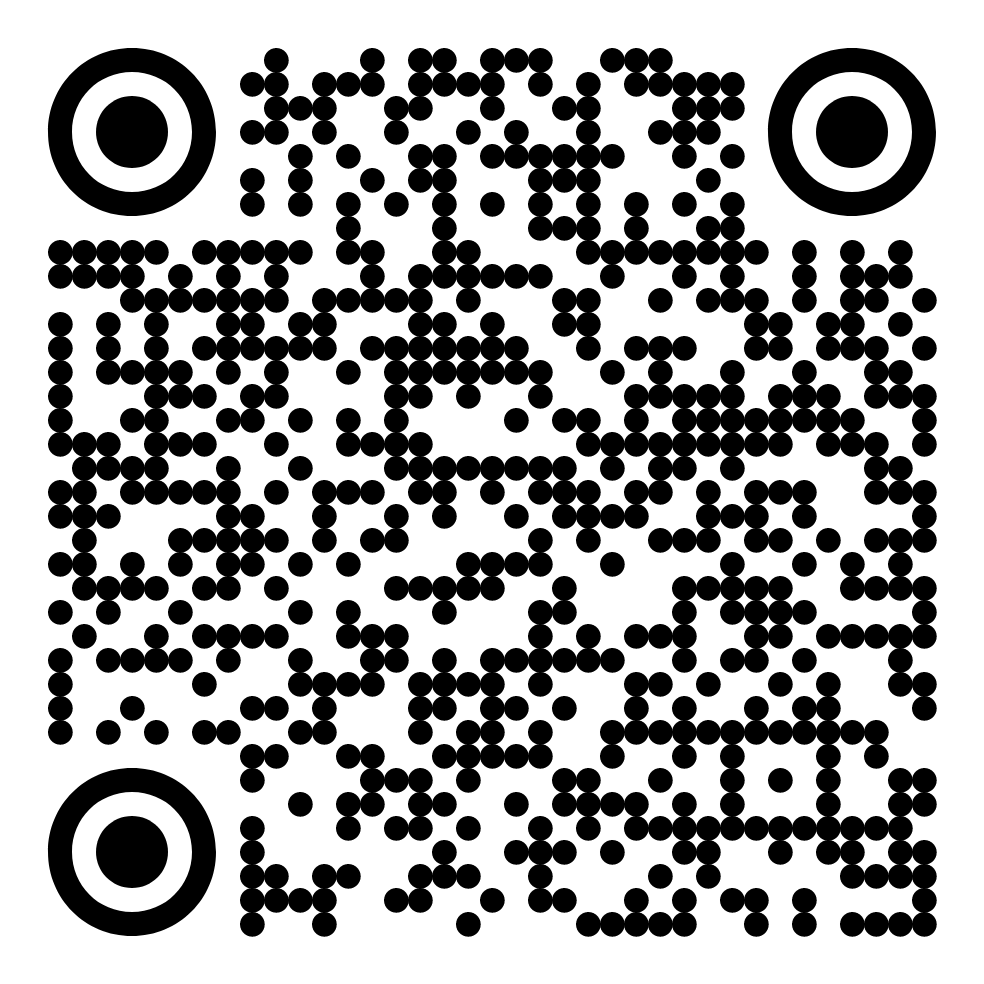
The dimensions shown may differ from those of the actual product.
* Requires iOS 13, iPadOS 13, ARCore 1.9 or higher.
* Requires iOS 13, iPadOS 13, ARCore 1.9 or higher.
Unboxed - IKB® Replacement
Any Questions?
We would be happy to show you solutions tailored to your process that limit the effects of an explosion to a harmless level and ensure that production can be resumed quickly after an explosion event.